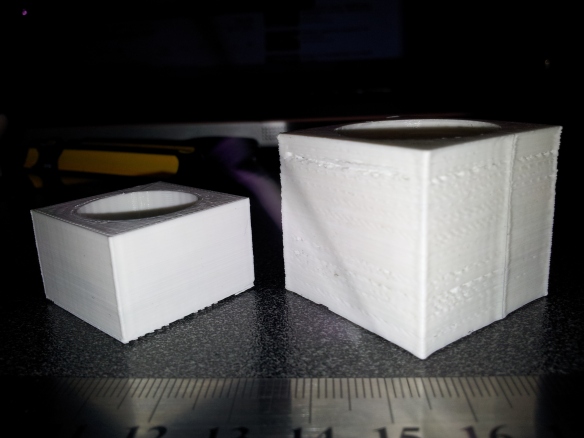
In using the machine I was able to calibrate and achieve near perfect prints with a balance of quality and speed. To achieve a perfect calibration a range of adjustments needed to be made to the printer physically, and to the software (Cura). Due to the Wooden frame of the printer, weather conditions affected the bed platform leveling making the bed either too low or too high; daily adjusted was needed to keep alignment. The stepper motors bands also needed to be tighten as loose bands will decrease accuracy and rods need to be well lubricated to ensure smooth movement of the nozzle. Software wise, adjusting Cura’s settings gave prints more refinement. Adjusting the layering thickness, temperature, speed, infill and retraction speed all contribute to high quality prints. Depending on the model these settings would have to be adjusted to fit to task at handThe machines extruder steps also had to be recalculate so layer steps, as seen in the picture ‘right cube’, weren’t missed and extruded evenly.
Left Cube: Achieving a high print quality calibration, 0.02mm
Print Specifications: Layering: 0.02mm, Temperature: 220 degrees, Infill: 60%, No support structure, Print Speed: 80mm/s, Retraction Rate: 40mm/s, Overlap 0.2mm, Filament Size: 2.85, Flow: 100%
Right Cube: Orignal Print quality
Print Specifications: Layering: 0.2mm, Temperature: 220 degrees, Infill: 60%, No support structure, Print Speed: 80mm/s, Retraction Rate: 80mm/s, Flow: 80%, Filament Size: 2.5