My first task was to print a replacement part for a plastic bracket used to mount a speaker which had snapped during use.

The broken speaker bracket (left) along with its slide on cover (right)
The first step was to replicate the part in a 3D modelling program. Using calipers and a ruler, I accurately measured and recreated the part in the parametric 3D modeller, Solidworks.

The speaker bracket modelled in CAD software.
It is worth noting that since I did not know precisely how the part was going to be used, I recreated all the features. Had I known which holes or bosses were not needed for example, I could have left them out of the 3D model.
The next step was to modify the part for improved strength. It was quite obvious where the part had failed and which area needed reinforcing. Nonetheless, I used a stress analysis tool on Solidworks to get a comprehensive look at stress occurring on the part when a load was applied. I then increased the size of the arms and ran the stress analysis tool again. Part stress was significantly reduced. This version of the speaker bracket was to be printed and tested for use.


Stress analysis before and after.
The part was printed on the Form1 printer which uses steroelithography technology which provides a much higher resolution than the cheaper extrusion printers. It’s estimated print time was 2 hours and 25 minutes while it’s total volume (including support material) was 15.7mL. So it is not exactly the fastest manufacturing method nor does it maintain 100% material usage efficiency since support material is discarded but this is more than made up for by the fact that there are ZERO tooling costs involved as well as negating the need to drive or travel anywhere to obtain the part, it can be created from the comfort of your own home.

The Form1 3D printer


The part ready for print on Form1’s software ‘PreForm’ (left) and the actual printed part (right)
The part was printed at printer’s lowest and thus fastest resolution of 0.1mm (it ranges from 0.1mm – 0.025mm). The print quality was stunning even on this setting and the tolerances were acceptable for such an application.
In an ideal world, prints could be used straight off the printer. Unfortunately though, that’s not the case. After coming off the machine, the print has to be soaked in a solution similar to methylates spirits for approximately 10 minutes and then the support material must be removed (roughly by hand at first then more precisely with the use of something such as the back edge of a stanley knife)

Peeling the support structure off the print.

The final part after removal of support material.
Success! The new printed part successfully fitted with the original plastic covering, including a fully functioning snap fit mechanism.




The original part alongside the new printed one.
Marcus Lee (UNSW)
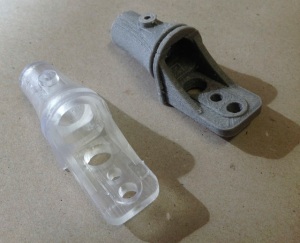